Alta’s co-founder and Chief Technology Officer, Derek Dorresteyn, is a motorcycle racer, and in his prime during the early 2000s, he was trying anything he could to squeeze more power and performance out of his YZ450F, but any gains he got somewhere, he lost elsewhere. Derek and his riding buddy Jeff Sand, another eventual co-founder and current Chief Development Officer, would get together and talk shop all the time, and they loved the idea of a smooth and perfectly responsive torque curve, but understood how difficult this was to achieve with a gas-powered bike.
So, with a few decades worth of fabrication, engineering and design expertise between the both of them, they started tinkering with the idea of building their own electric motorcycle, a motorcycle that could not only deliver power in a way in which a gas bike couldn’t, but a bike that could be easier to ride, too. In 2007, the first sketches of the original Redshift started coming together on bar napkins in San Francisco.
Enter Marc Fenigstein, the company’s third co-founder and current CEO. Between the three of them, they had the vision and means to create Alta, and Alta Motors was conceived on October 21, 2010 after a few rounds of whiskey – a story as old as time.
We got the opportunity to check out and tour Alta’s whole operation in Brisbane, CA, a small town just south of San Francisco, and below are ten cool/neat/interesting things we saw while there. Enjoy.
The “OG” first Redshift and the Alta Family Tree
Every story has its beginning, so let’s start there with the first Alta Redshift prototype. This first Redshift was a mishmash of a few different dirtbike parts, but the core was all Alta. The battery, motor, front and rear bulkheads, which serve as the motorcycle’s primary chassis, aren’t all that different from the first generation of production Redshift models. This “OG” Redshift is of course much less refined than what would roll off an OEM production line, but it’s incredibly impressive for three guys working out of a garage.
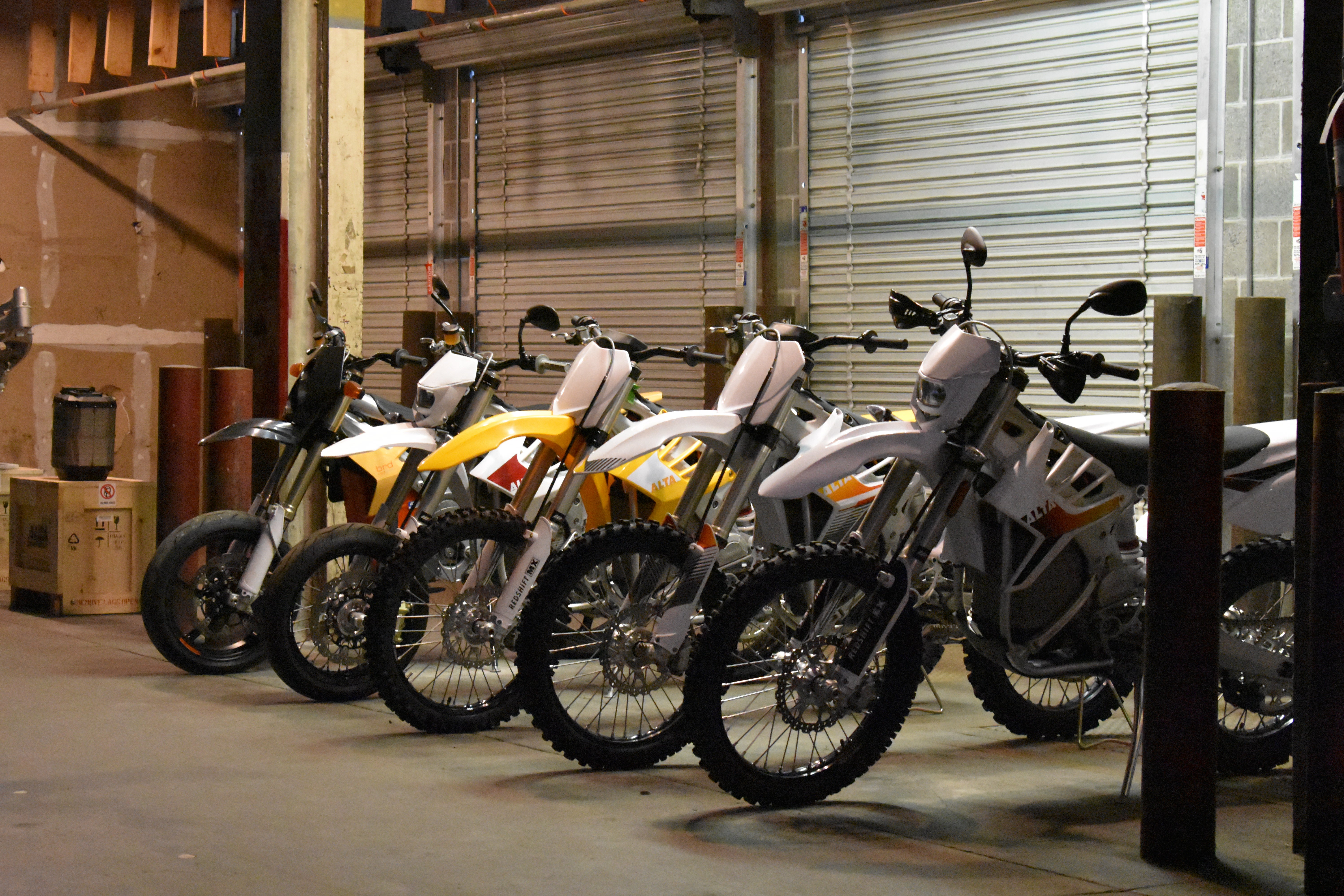
98% of Alta Employees Ride
Alta has less than 100 total employees, which by my math means there’s only one worker who’s either holding out on riding, or is physically unable to do so. Of the 90-something people that work there, more than half are engineers and just about everybody either rides their motorcycles to work, or they pedal their bicycles. But everybody is in one shape or another a motorcycle enthusiast.
Weekend Loaner Bikes
One of the perks of working at Alta is that they have a loaner fleet of bikes that anyone can check out over the weekend to go out and ride. As you might expect, Alta’s employees take full advantage of this – why wouldn’t you? – and there’s very few bikes left on Friday afternoons. It’s great because not only are the employees becoming better acquainted with the motorcycles they’re building and selling, but it also serves as another form of in-house R&D.
The Assembly Line
Just about every step of the design, manufacture and assembly process is done under one roof in Northern California’s Bay Area. The assembly line is designed to run with just eight skilled technicians and they can build 10 Redshifts a day in Alta’s Brisbane, CA factory. They’ve optimized each station to be balanced for cycle time, using tablets with step-by-step work instructions, with associated part numbers, torque requirements and quality control notes. Their assembly process is as simple as it gets.
Tool Stations
Each tool station along the assembly line has only the tools you need and none you don’t, which leaves very little room for error. Even the drills and impact drivers are wirelessly synced to know which drill bits they’re using and what torque spec to tighten to. Once tightened, the drill then sends the torque spec down to the degree of rotation after seating to a database that houses each and every single piece of information pertaining to each individual bike ever made. If there’s ever any sort of issue or malfunction, by looking up the bike’s VIN, Alta can pull up just about anything about the bike’s build history to help determine and fix the problem.
Front and Rear Bulkhead
Derek explained John Britten’s theory of part engineering, which included that each and every motorcycle part needs to serve at least two purposes. John Britten was a legendary motorcycle mechanical engineer and designer from New Zealand who built the Britten V1000 that went on set numerous world records.
Following Britten’s model, Derek explained that the rear bulkhead serves at least 10 different roles. The rear bulkhead functions as one of the Redshift’s structural hubs, serving as the bike’s chassis core, outer motor casting, cooling circuit for the motor and inverter as well as the transmission case for the gear reduction – just to name a few.
The front bulkhead is made from forged 6061-T6 aluminum alloy. It not only forms the front of the Redshift chassis, but also acts as a heat sink for the Redshift system with cooling lines running throughout.
Stress Testing Table
Each piece Alta designs is engineered to exhibit extreme tolerance in the most severe conditions so riders remain safe and bikes maintain their integrity. The steel structure you see above is something Alta is in the process of building to try and destroy each component they make. The table will be used as an anchor to crank down on bikes’ frames and chassis to the point of failure to see just how much shear strength and tensile force is needed to compromise certain parts. Alta also performs a drop test on its bikes by kissing them goodbye off a four-story platform. When testing against other OEM’s bikes, Alta claims theirs are much stronger and resistant to damage than other manufacturers’, especially when dropped from 40+ feet.
The Dyno
Every bike is quality-control tested on the dyno to make sure everything is up to snuff in the power delivery department. One thing we learned was that due to fewer moving parts and the reduction, or almost total elimination, of engine wear compared to a gas-burning motorcycle, an Alta continues to make and deliver the same amount of power and torque over the course its lifespan. Alta claims that they dynoed one of their bikes that had 300 hours on it and it delivered the same output numbers as it did off the assembly line. They were able to verify this thanks to their comprehensive database of each and every individual spec and number tied to each bike’s VIN. Additionally, the Redshift’s service interval is every 1,000 hours (save for typical wear parts like chains, sprockets, brake pads and tires).
Jeffrey Carver Jr. Flat Tracker
Jeffrey Carver Jr. is a top-10 American Flat Track racer who’s no stranger to finishing on the podium, and he’s been riding and testing a special Alta Redshift flat tracker in his free time. Carver normally competes in the AFT Twins class, but could potentially be racing this Alta in the AFT Singles class as well. Alta is committed to racing their motorcycles because they believe racing is the true benchmark of progress as well as a clear marker of where the company stands relative to its gas-powered rivals.
Concept Flat Tracker
This is the first thing you see when you walk into Alta HQ and the last when you leave. With its minimal bodywork and carbon fiber wheels, it’s one slick ride. Alta’s whole deal is to build motorcycles that make you tingle when you look at them, giggle when you ride them, and even scare you just a little bit. This bike is essentially a motor with handlebars – everything else is a light and minimal as possible. Altas normally come with the option to flip through four different map settings from mild to wild. This one is specially programed to only run in map four, or the “Overclocked” map as Alta calls it. This map gives you all of the motor’s 50 ponies, which might not sound like a lot, but paired with its 147 lb-ft of torque and the bike’s light weight, you’ll want to make sure you’re hanging on when you crack the whip.